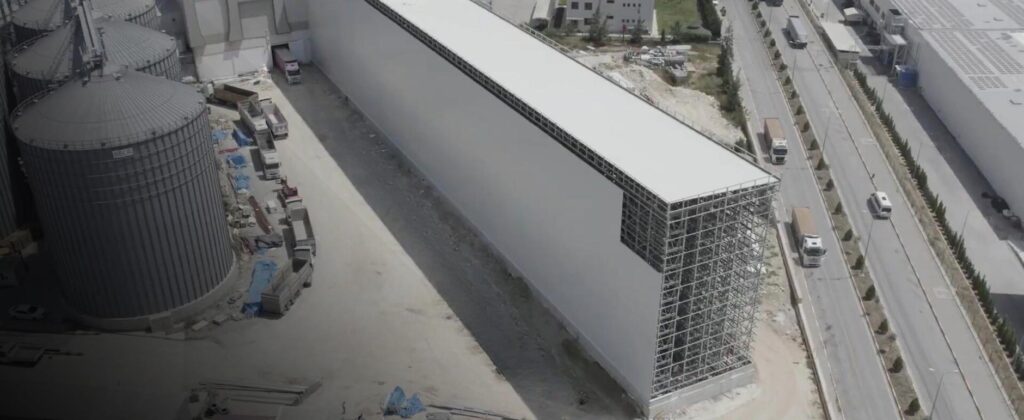
ÜÇGE DRS serves with the concept of Innovative Warehouse Solutions;
a national and international company in logistics, retail and all branches of industry
Heavy and light load warehouse shelving systems and smart products specially designed for many companies
produces projects with storage solutions.
They are innovative systems used to optimize storage areas and increase efficiency.
It provides a flexible storage solution for warehouses requiring low volume and low mobility.
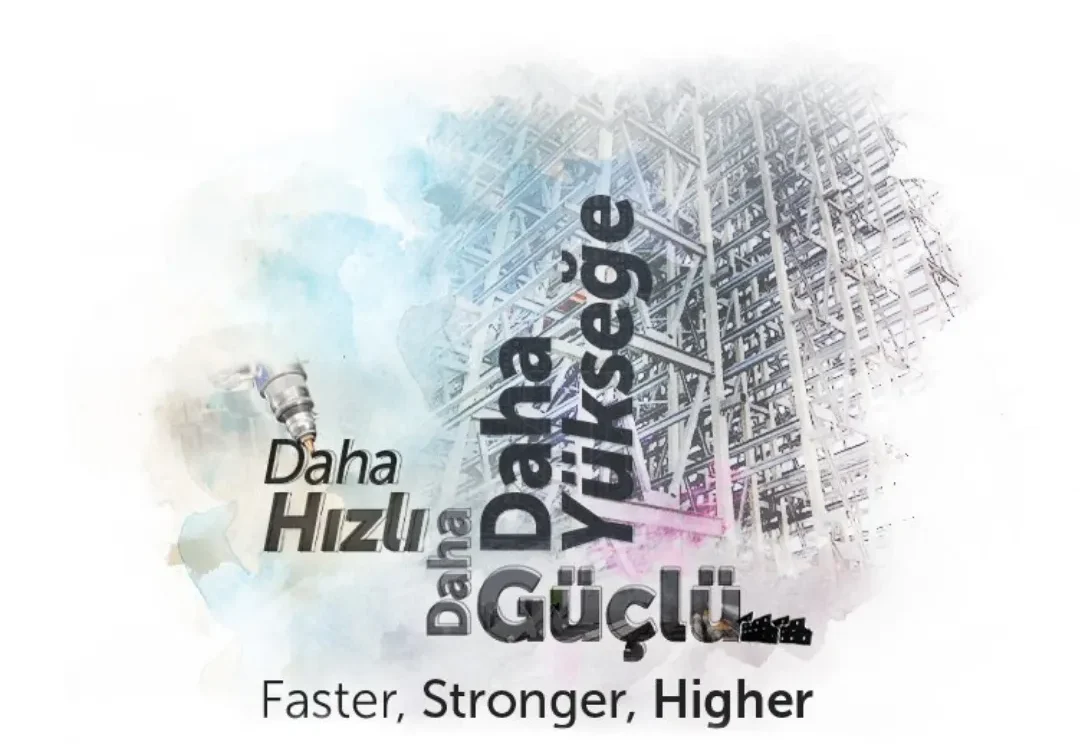
ÜÇGE Warehouse Racking Systems is a company that offers innovative and high-quality storage solutions. The company, which has a leading structure with the 'firsts' it has created in the sector, implements important projects every year with its R&D department. It carries out successful projects within the scope of TÜBİTAK, BEBKA, TURQUM and SME support.
With its customer-oriented approach, industry-leading technologies and expert team, it offers customized solutions for storage needs. Its goal is to increase customers' operational efficiency, optimize storage space and reduce costs. Its priority is to keep customer satisfaction at the highest level with products that combine reliability, durability and performance.
Warehouse Racking Systems
Automated
Warehouse Racking Systems
Systems that increase storage efficiency, reduce errors and optimize business processes
Manual
Warehouse Racking Systems
Flexible storage solution for warehouses requiring low volume and low mobility
Semi Automated
Warehouse Racking Systems
Innovative mobile systems used to optimize storage spaces and increase efficiency
Special
Warehouse Racking Systems
Systems that offer warehouse shelving solutions for innovative and special needs
Automatic Warehouse Racking Systems
Frequently Asked Questions About AS/RS
AS/RS stands for Automated Storage and Retrieval Systems. These systems are used to automate storage processes and increase efficiency. AS/RS usually includes automated handling systems with storage areas consisting of high shelves. Automatic transport vehicles take products from shelves, move them and place them in the desired sections. It optimizes operations by working integrated with the warehouse management system.
- High storage capacity: AS/RS ensures maximum use of storage space with high shelves and automatic transport vehicles.
- Fast and accurate storage: Automatic transport vehicles quickly store products and place them in the right places, minimizing human errors.
- Labor efficiency: AS/RS reduces labor needs and provides a more efficient business by minimizing human dependency in operations.
- Simultaneous operations: AS/RS can handle multiple operations simultaneously, which helps speed up warehouse processes.
- Warehouse management: AS/RS works integrated with warehouse management systems and provides control over issues such as inventory tracking, order management and operational efficiency.
AS/RS systems are used in many industries. It is frequently preferred especially in sectors that need high volume storage and want to increase warehouse efficiency. Industries such as automotive, e-commerce, retail, food and beverage, pharmaceutical, logistics and distribution are adopting AS/RS systems. These systems can be used in large storage facilities, distribution centers or manufacturing facilities.
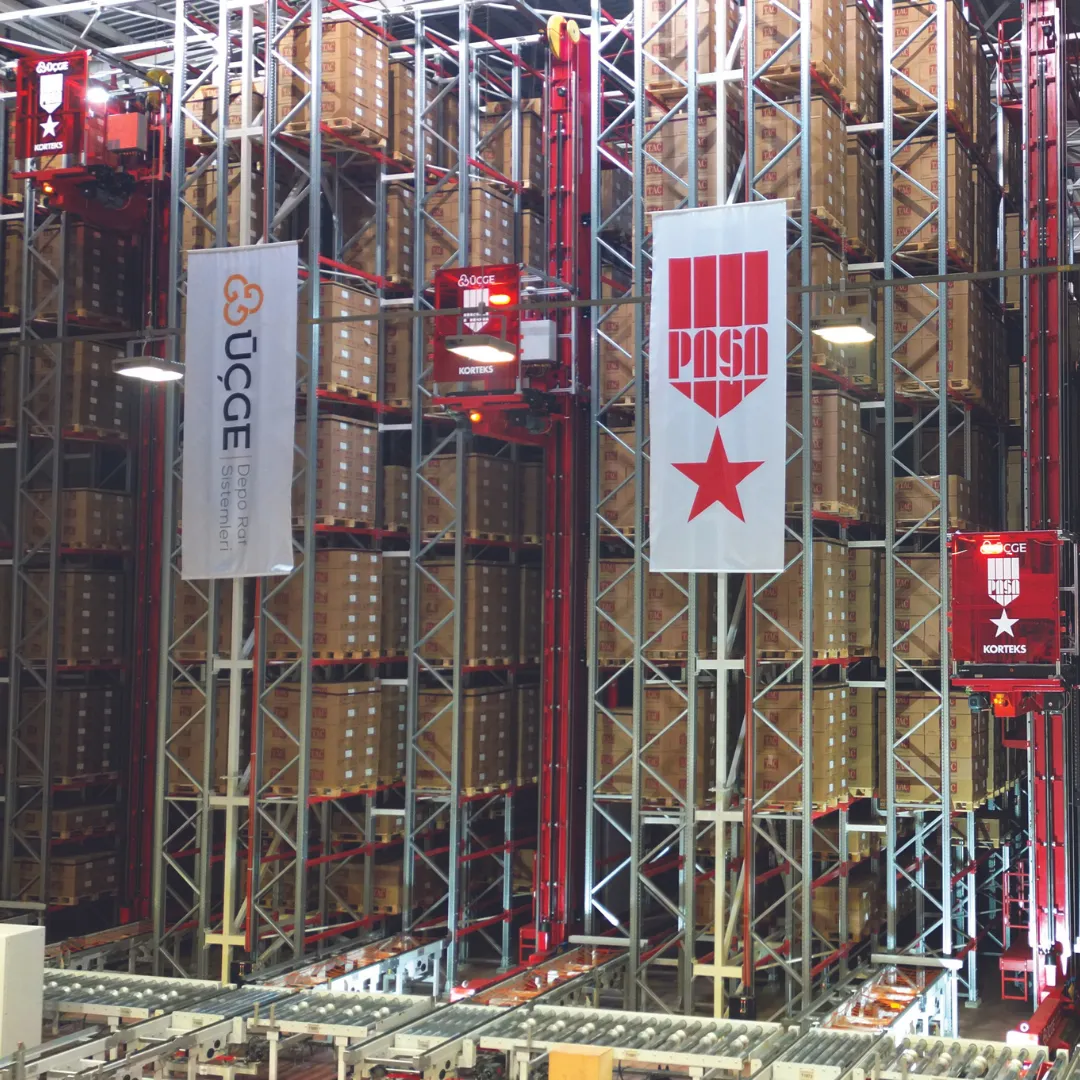
Innovative shelving system solutions
Case Study
We can be a part of your success too. Contact now.
News
Follow us for our achievements, awards and the latest news about us.